Business Documentation and Quality Control: Essential Elements for Company Success
Understanding business documentation and quality control
Every successful business rely on proper documentation and effective quality control measures to achieve its goals. These elements form the backbone of organizational structure and operational efficiency. This article explores the essential business documents that summarize a company’s business plan and examine the critical business function responsible for quality control during manufacturing and distribution processes.
Key business plan documents
A comprehensive business plan typically consist of several documents, but two stand out as the about crucial for summarize a company’s overall business strategy and objectives.
Executive summary
The executive summary is one of the about important documents that summarize a company’s business plan. Despite being place at the beginning of a business plan, it’s typically write concluding to ensure it capture the essence of the entire plan. This concise document (commonly 1 2 pages )provide a high level overview of the company’s:
- Mission statement and vision
- Company description and core values
- Market opportunity and target audience
- Products or services offer
- Competitive advantages
- Financial highlights and projections
- Current stage of development
- Funding requirements (if applicable )
The executive summary serve as a snapshot of the entire business plan, make it invaluable for potential investors, partners, or other stakeholders who need to quickly understand the company’s direction and potential. It must be compelling sufficiency to encourage readers to explore the full business plan.
Business model canvas
The second essential document that efficaciously summarize a business plan is the business model canvas (bBMC) Develop by alAlexandersterwalder, this strategic management tool provide a visual chart with elements describe a company’s value proposition, infrastructure, customers, and finances. The bmBMConsist of nine building blocks:
- Value propositions: The products and services that create value for specific customer segments
- Customer segments: The different groups of people or organizations the company aim to reach and serve
- Channels: How the company communicate with and reach its customer segments to deliver its value proposition
- Customer relationships: The types of relationships establish with specific customer segments
- Revenue streams: How the company generate income from each customer segment
- Key resources: The about important assets require making the business model work
- Key activities: The about important things the company must do to make its business model work
- Key partnerships: The network of suppliers and partners that make the business model work
- Cost structure: All costs incur to operate the business model
The business model canvas provides a comprehensive yet concise overview of how a company create, delivers, and capture value. Its visual formatmakese it easier for stakeholders to understand the business strategy at a glance, make it an excellent complement to the more narrative focus executive summary.
Quality control in business operations
While proper documentation establish a company’s direction, effective quality control ensure that products and services meet the standards promise to customers. Let’s examine the business function responsible for maintaining quality standards during manufacturing and distribution.
Operations management: the key to quality control
The business function that help ensure quality control during manufacturing and distribution is operations management. This critical function oversees the production of goods and services, manage the processes that transform inputs( raw materials, labor, energy) into outputs ((inish products or services ))
Operations management is responsible for design, implement, and monitor quality control systems throughout the production and distribution chain. This function ensure that products systematically meet specifications, comply with regulations, and satisfy customer expectations.
Key quality control responsibilities of operations management
Operations management handle several essential quality control activities:

Source: photodune.net
1. Quality planning
Before production begin, operations management establish quality standards, objectives, and processes. This includes:
- Define product specifications and quality metrics
- Establish acceptable tolerance levels
- Develop inspection procedures
- Create quality documentation systems
- Set up quality management systems (like iISO9001 )
2. Quality assurance
Operations management implement systems to prevent defects from occur during production:
- Train employees on quality standards and procedures
- Implement process control
- Conduct regular audits of production processes
- Manage supplier quality
- Ensure adherence to good manufacturing practices (gGMP)
3. Quality control
During production, operations management perform inspections and testing to identify and address defects:

Source: dreamstime.com
- Conduct in process inspections
- Perform statistical process control
- Test samples against specifications
- Identify and segregate non-conforming products
- Implement corrective actions for quality issues
4. Quality control in distribution
After production, operations management continue quality oversight during distribution:
- Ensure proper packaging to prevent damage
- Verify appropriate storage conditions
- Monitor transportation conditions (temperature, humidity, etc. )
- Implement track and trace systems
- Conduct final inspections before shipment
- Manage product recall if necessary
Quality control methodologies in operations management
Operations management employ various methodologies to ensure quality control throughout manufacturing and distribution:
Six sigma
This data drive methodology aim to eliminate defects by reduce process variation. Six sigma use the DMAIC approach (define, measure, analyze, improve, control )to identify and address quality issues. Companies implement six sigma aim for no more than 3.4 defects per million opportunities.
Lean manufacturing
Focus on eliminate waste while maintain quality, lean principles help operations management streamline processes and enhance quality control. Techniques like 5s (sorting, set in order, shine, standardize, sustain )create organize workspaces that reduce errors and improve efficiency.
Total quality management (tTQM)
TQM is a company-wide approach that make quality everyone’s responsibility. Operations management implement TQM by foster a culture of continuous improvement, customer focus, and employee involvement in quality processes.
Statistical process control (sSPC)
SPC use statistical methods to monitor and control production processes. Operations management employ control charts and other statistical tools to identify when processes are drift from specifications, allow for timely corrections.
Technology in quality control
Modern operations management leverage various technologies to enhance quality control:
- Automated inspection systems: Use cameras, sensors, and AI to detect defects more accurately than human inspectors
- Quality management software: Centralize quality data, documentation, and corrective actions
- Internet of things (iIOT) Deploy connected sensors throughout production and distribution to monitor quality parameters in real time
- Blockchain: Ensure transparency and traceability throughout the supply chain
- Predictive analytics: Identify potential quality issues before they occur by analyze patterns in production data
The integration of business planning and quality control
The executive summary and business model canvas provide the strategic framework for a company’s operations, while operations management implement the quality control measures necessary to deliver on those strategic promises. This integration is essential for business success.
Strategic alignment
Quality control objectives must align with the overall business strategy outline in the business plan documents. For example:
- If the business strategy emphasizes premium quality as a competitive advantage, operations management will implement more stringent quality control measures
- If cost leadership is the strategy, operations management will focus on quality control methods that will minimize waste and rework while will maintain acceptable quality levels
- If innovation is key, operations management will develop quality control processes flexible sufficiency to will accommodate rapid product changes
Financial impact
Effective quality control by operations management direct impact the financial projections outline in the business plan:
- Reduced waste and rework improve profit margins
- Fewer returns and warranty claims decrease costs
- Consistent quality build brand reputation, potentially allow for premium pricing
- Improved efficiency through quality processes can reduce production costs
Customer satisfaction
The customer segments identify in the business model canvas expect consistent quality. Operations management’s quality control function ensure that products meet or exceed customer expectations, lead to:
- Higher customer retention rates
- Positive word of mouth marketing
- Increase customer lifetime value
- Stronger brand loyalty
Conclusion
Understand the key documents that summarize a business plan — the executive summary and business model canvas — provide insight into a company’s strategic direction. Likewise, recognize operations management as the business function responsible for quality control during manufacturing and distribution highlight the importance of operational excellence in deliver on strategic promises.
Unitedly, these elements form a comprehensive framework for business success. The business plan documents establish what the company aim to achieve, while operations management’s quality control function ensure that the company systematically deliver products and services that meet or exceed customer expectations.
For businesses look to improve their performance, invest in both clear strategic documentation and robust quality control processes is essential. By align these elements, companies can build a foundation for sustainable growth, customer satisfaction, and competitive advantage in their respective markets.
MORE FROM ittutoria.net
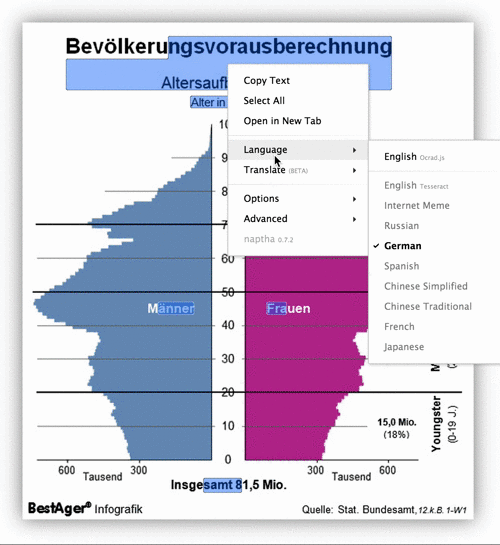
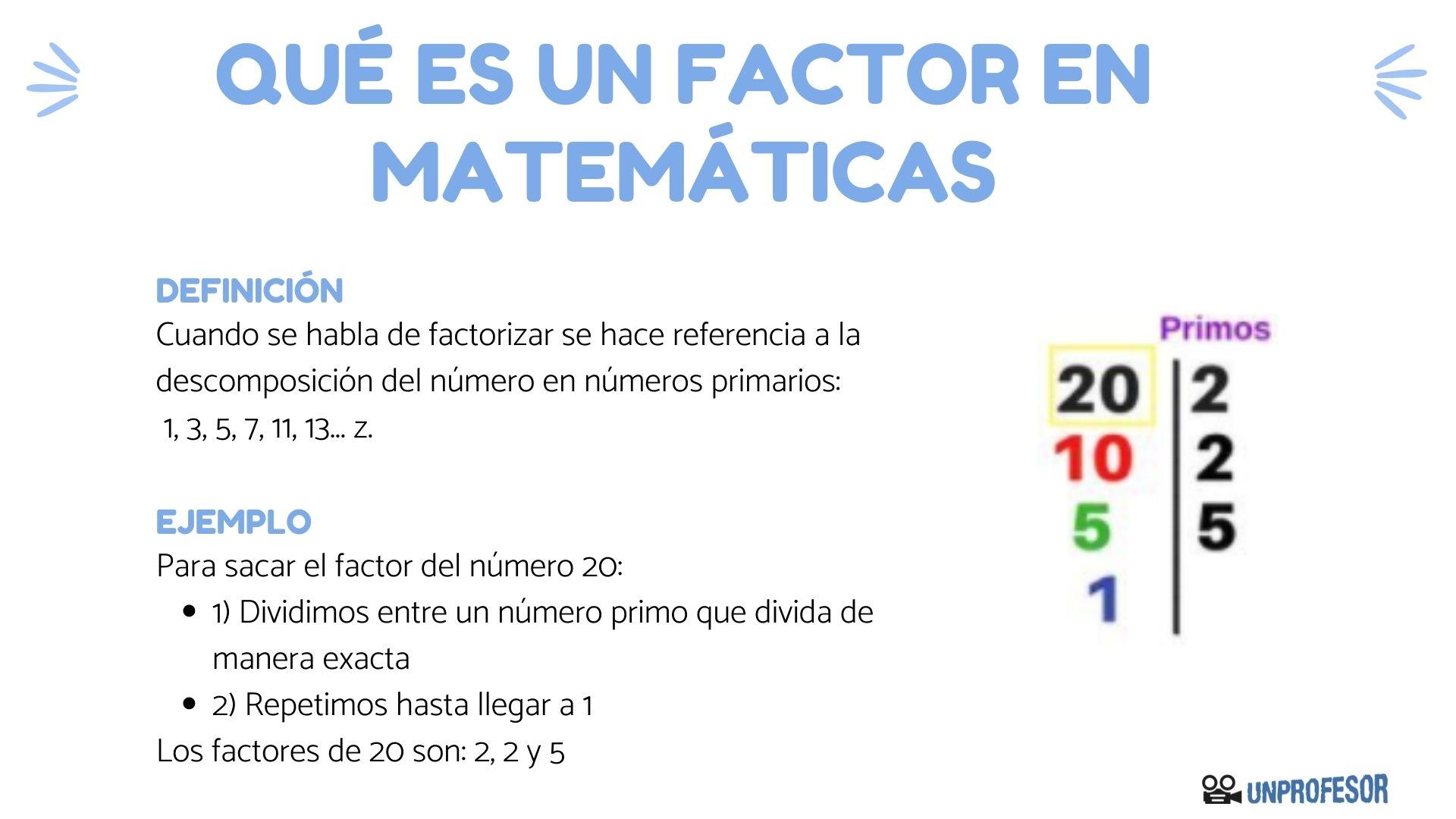
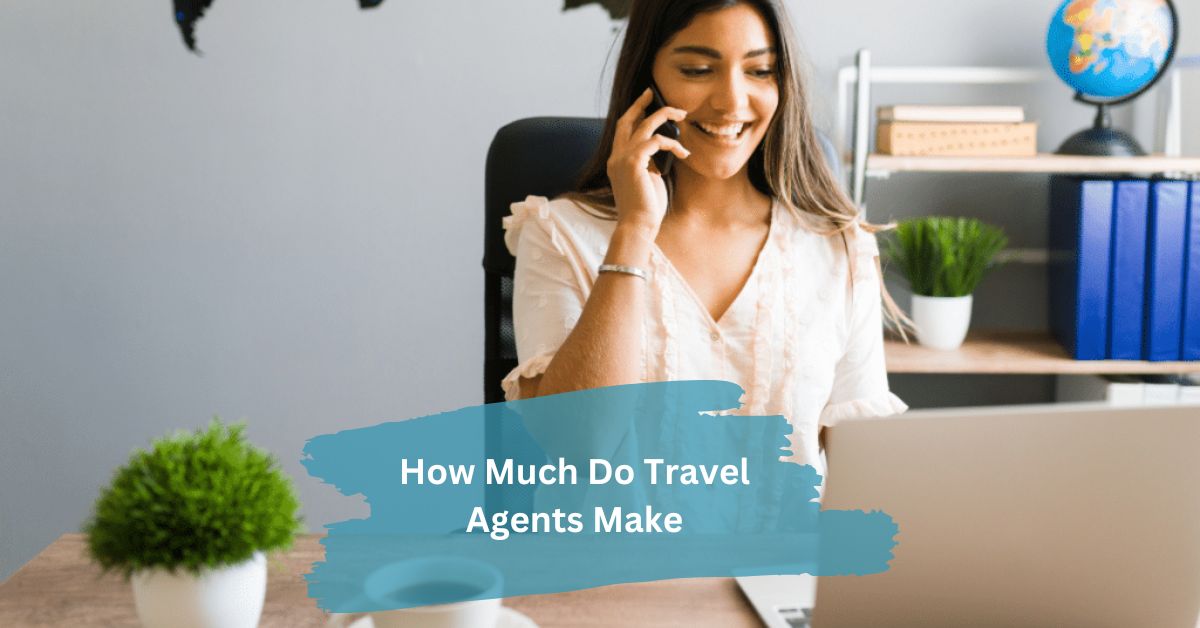
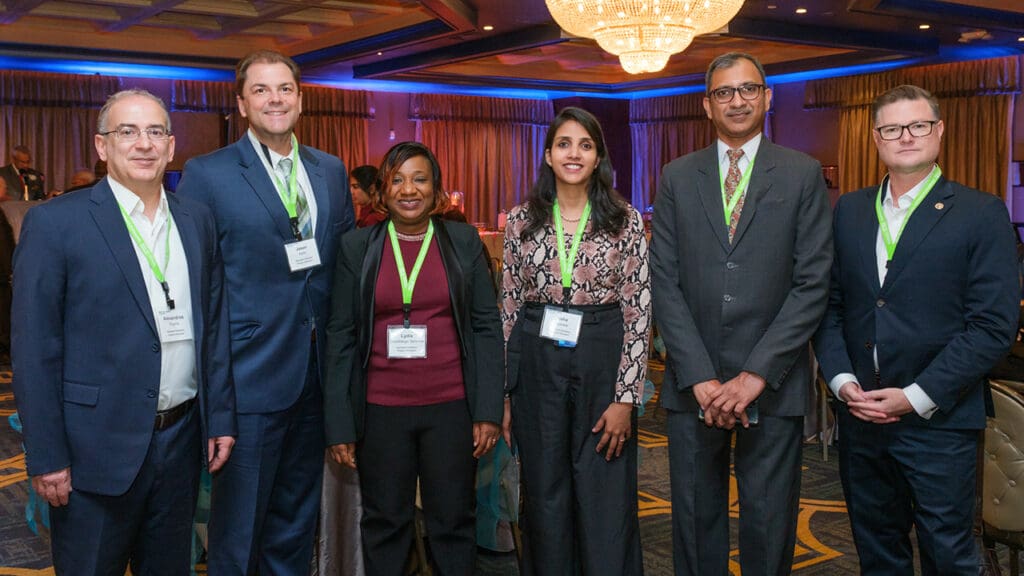
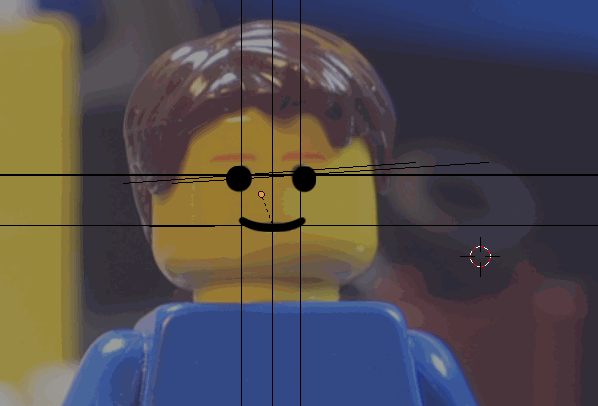
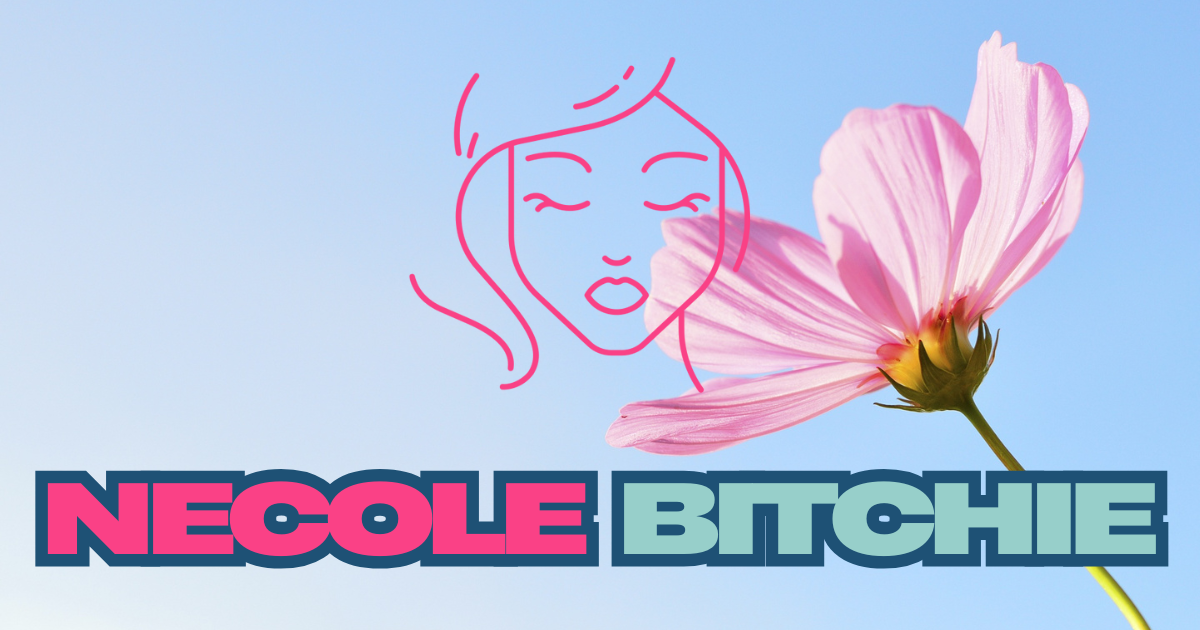
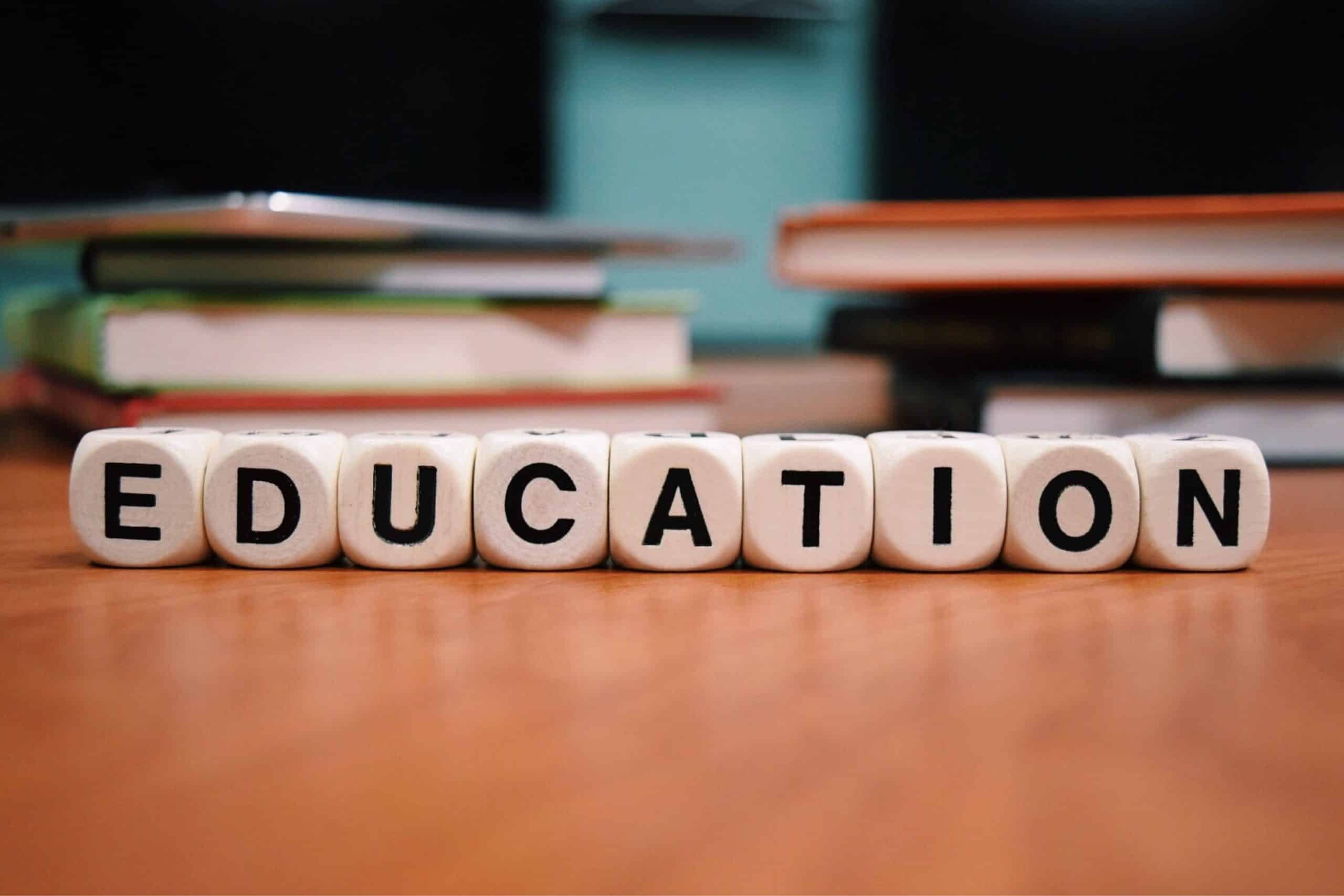
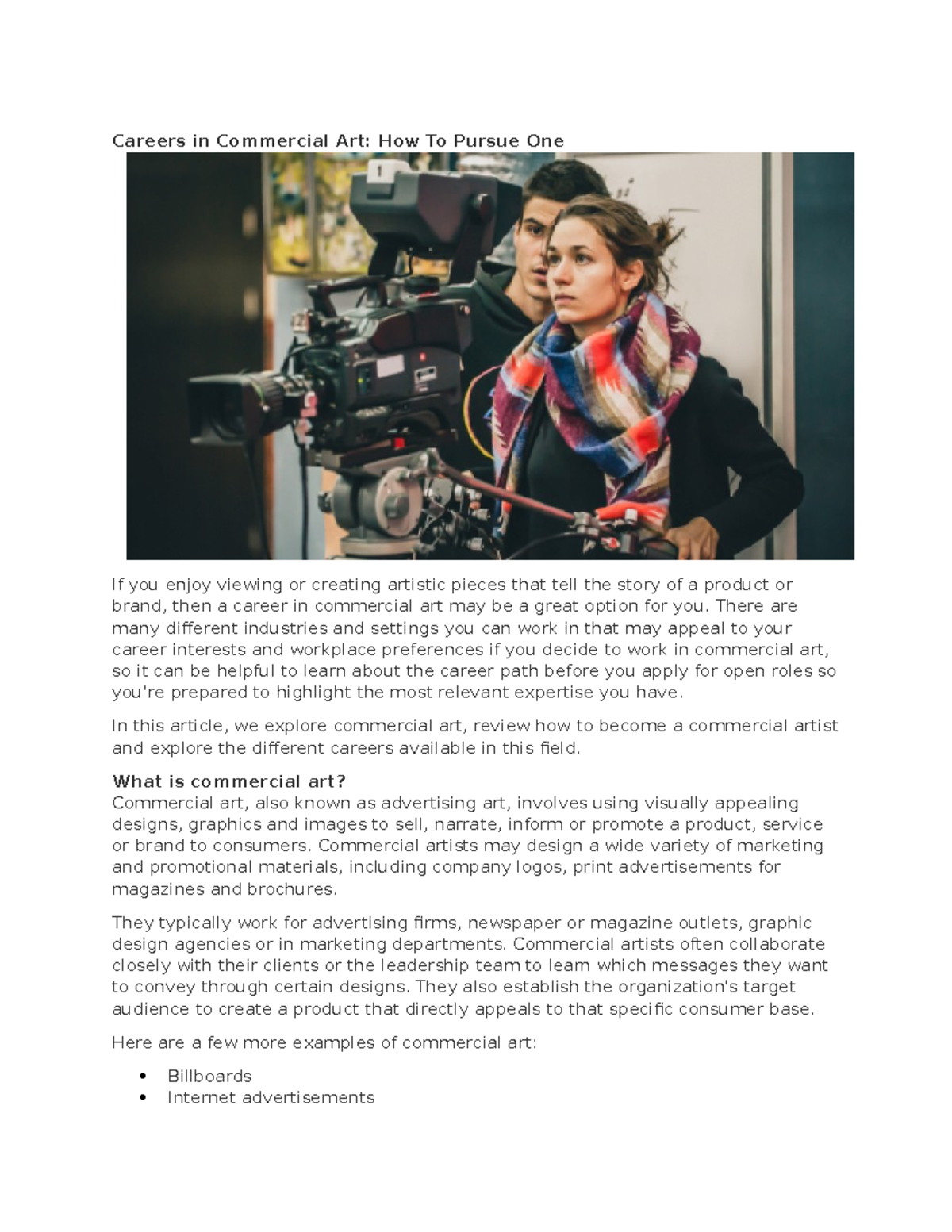
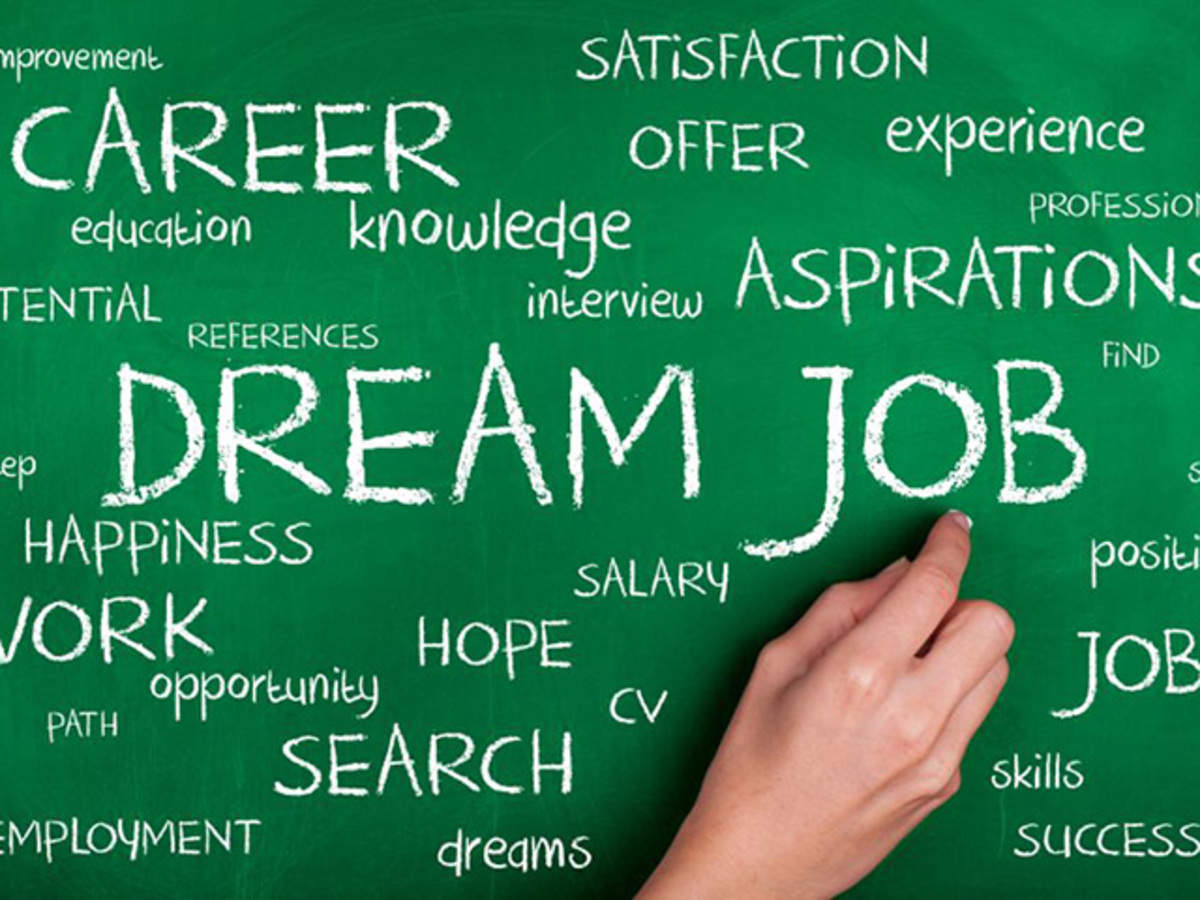
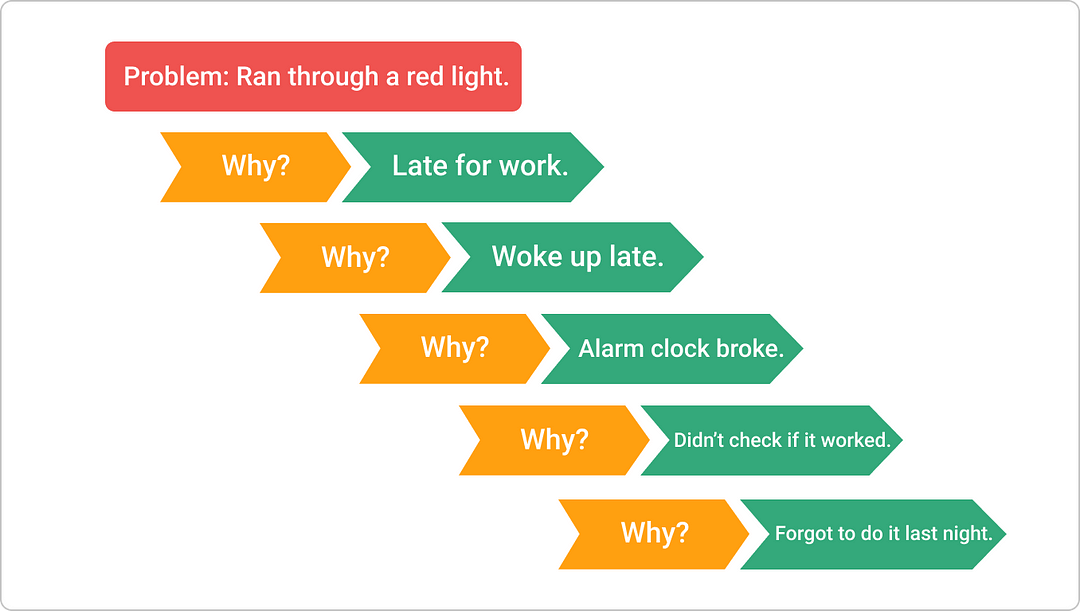
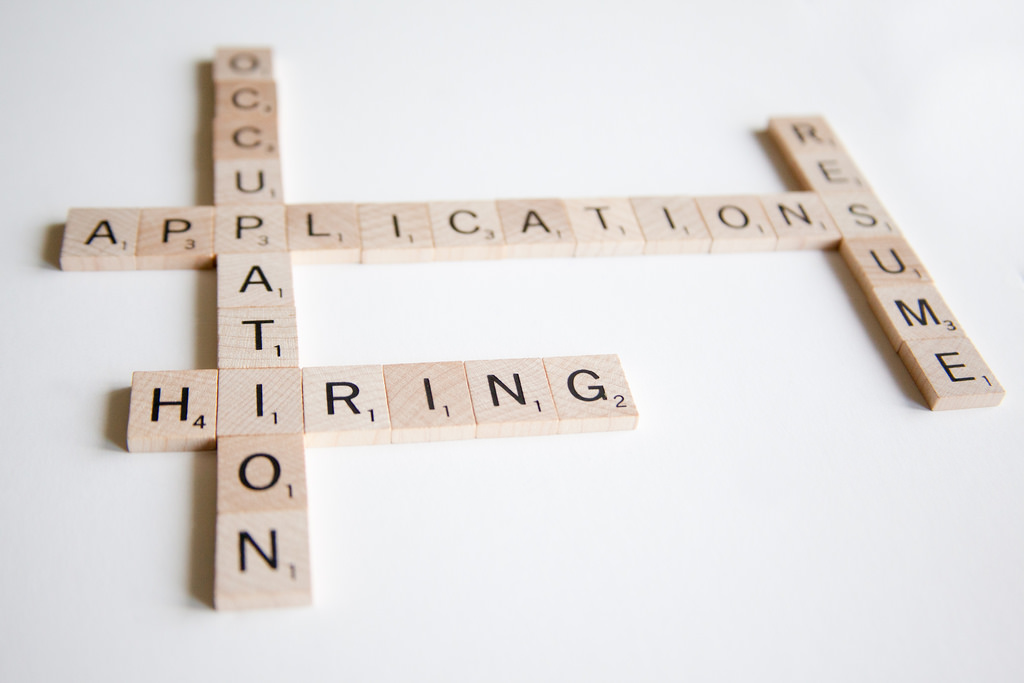
